En esta entrevista, aprendemos cómo el área de Técnica y Producción (T&P) de Nestlé Colombia Ecuador está utilizando Lean y el marco de los cuatro tipos de problemas de Art Smalley para acercar el liderazgo al gemba.
Entrevistados: María Fernanda Avellaneda, Gerente de Estrategia de Manufactura, y Fabio França, Vicepresidente Técnico Regional, T&P Nestlé Colombia Ecuador.
Planet Lean: Las grandes empresas suelen tener mucha experiencia en la implantación de metodologías de mejora. ¿En qué punto se encuentra T&P Nestlé Colombia Ecuador en su viaje de mejora?
María Fernanda Avellaneda: Llevamos unos diez años trabajando con nuestro sistema interno -Nestlé Continuous Excellence- (a nivel global, la organización lleva mucho más tiempo utilizándolo). En lo que respecta a nuestras operaciones de fabricación, tenemos dos enfoques principales que coexisten dentro de la NCE: la Gestión del Rendimiento Total (TPM) y el Pensamiento Lean. De los dos, el Lean es sin duda el “nuevo”, ya que se introdujo en nuestros procesos hace unos tres años.
Nuestra ambición en T&P es lograr una transformación cultural y desarrollar las capacidades de nuestro personal de primera línea, para que sean más autónomos en su capacidad de resolver problemas. Sin duda, hemos empezado a ver progresos en esa dirección, aunque la mayoría de nuestras líneas todavía tienen un largo camino que recorrer antes de alcanzar el nivel de autonomía que deseamos. De lo que nos hemos dado cuenta es de que para que este proceso de transformación se produzca necesitamos la presencia constante del liderazgo en la planta, para acompañar a nuestra gente. Y hemos estado luchando con eso: las reuniones y los problemas cotidianos se interponen en el camino y mantienen a los líderes alejados de la gemba, frenando el progreso de nuestra transformación.
PL: ¿Cómo interactúan el TPM y el Lean en NCE?
Fabio França: Cada empresa tiene su sistema de mejora. La nuestra siempre ha sido NESTLE CONTINUOUS EXCELENCE – NCE (TPM en la fabricación y Lean Thinking para toda la cadena de valor). Recuerdo que cuando decidimos introducir el Lean en nuestras fábricas de Brasil, inicialmente empezamos aplicando el TPM en un sitio y el Lean en otro. Cuando intentamos juntar los dos, comprendimos que habíamos cometido un gran error: la gente de ambos sitios estaba contenta con los sistemas que tenían y era reacia a adoptar el otro. Fue entonces cuando nos dimos cuenta de que no era necesario mantener separados el TPM y el Lean. Sus principios y herramientas son muy similares.
El TPM hace hincapié en la maquinaria, y el Lean en el concepto más amplio de eliminación de desperdicios. Encajan perfectamente. En última instancia, lo único que importa es el resultado para nuestros consumidores y en Nestlé intentamos pensar en términos de oportunidades de negocio más que en las metodologías que utilizamos para buscar esas oportunidades.
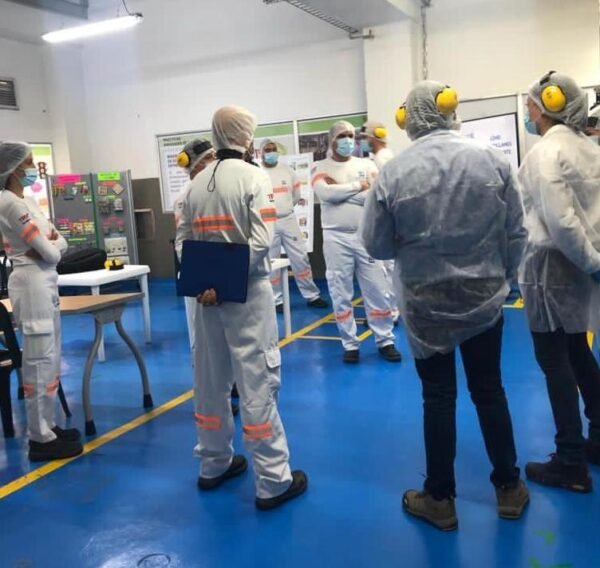
Paseo por el Gemba con el Lean Institute Colombia
¿Cómo les ayuda el Lean a acelerar el ritmo del cambio?
FF: El Lean Thinking apoya nuestros esfuerzos por transformar la cultura en Nestlé Colombia Ecuador. Nos proporciona una visión más holística de nuestro trabajo y nos ayuda a identificar oportunidades de negocio para mejorar en toda la cadena de valor. Nos está haciendo a todos mejores hombres y mujeres de negocios.
MFV: Aunque nuestras conversaciones siguen centrándose principalmente en el TPM, no cabe duda de que el Lean está empezando a hacer su aportación. ¿Cómo? Durante el Lean Summit 2019 organizado por el Lean Institute Colombia, escuchamos sobre los cuatro tipos de problemas que Art Smalley esboza en su más reciente libro. Lo vimos como una oportunidad para aclarar las responsabilidades de resolución de problemas de las personas en los diferentes niveles de la organización y decidimos hacer un experimento en nuestras seis fábricas.
Los miembros del “equipo de mejora” no necesitábamos que nos convencieran, pero queríamos asegurarnos de que las personas de todas las fábricas nos acompañaran en este viaje de descubrimiento. Por eso creamos un equipo multifuncional para trabajar en este experimento.
Nuestro primer paso fue analizar nuestro enfoque de la gestión utilizando el Marco de Transformación Lean (LTF). Pudimos ver que todos los elementos de la “casa” estaban ahí, pero decidimos desafiarnos a nosotros mismos para entablar conversaciones más centradas en nuestro sistema de gestión y en cómo estaba influyendo en nuestra transformación. Hablar de los distintos tipos de problemas y de quién es responsable de ellos dio lugar a conversaciones constructivas y a la identificación de numerosas oportunidades de mejora.
Lean nos ha permitido aprovechar nuestro trabajo con la Gestión del Rendimiento Total con un nuevo enfoque en el valor del cliente y en la consecución de la autonomía de nuestros equipos de primera línea. De hecho, diría que TPM y Lean son totalmente complementarios.
PL: ¿Qué puede decirnos sobre el papel del liderazgo en la transformación?
FF: Lean nos está enseñando un enfoque diferente del liderazgo, que se plasma en el concepto de paseo por la gemba y que hace hincapié en la observación, la escucha activa y la comprensión profunda del trabajo. No basta con asegurar que cumplimos nuestros objetivos de producción; es fundamental que averigüemos en qué condiciones se cumplen esos objetivos, para poder mejorar el proceso y, en última instancia, conseguir mejores resultados. Para ello, debemos ser líderes humildes y serviciales.
PL: ¿Puede hablarnos más de su trabajo con los cuatro tipos de problemas?
MFA: De todas las ideas Lean que hemos aplicado, ésta es una de las más impactantes. Nuestro análisis reveló que muchos de nuestros líderes estaban trabajando en los problemas de tipo 1 y 2 (resolución de problemas y diferencias con respecto a la norma), a pesar de que éstos deberían ser una prerrogativa de la primera línea. Esto los mantenía alejados del gemba. A la luz de esto, uno de nuestros objetivos es comprender qué debemos ofrecer a nuestros empleados para que sean más autónomos. ¿Se trata de más formación? ¿Coaching? ¿Objetivos diferentes y quizás más desafiantes?
La categorización de los “cuatro tipos” de problemas fue una gran adición a nuestro arsenal de herramientas y técnicas e hizo que nuestro sistema de gestión fuera más ágil. Definir claramente los problemas significa asegurarse de que las personas adecuadas asumen la responsabilidad de las cosas correctas. (Incluso hemos diseñado una formación basada en los cuatro tipos de problemas y hemos introducido el tratamiento de problemas con el A3 para dar a las personas una herramienta adicional que puedan utilizar en su trabajo).
Cuando pedimos a los operarios que compartieran su opinión, lo que aprendimos fue esclarecedor y muy satisfactorio. Nos dijeron que los líderes les retaban ahora a plantear problemas y a responsabilizarse de ellos. Hablaron de la proximidad del liderazgo a la planta, desafiándonos implícitamente a continuar con esto en el futuro. El hecho de que los directores de fábrica pasen tiempo en el taller y se tomen esta parte de su trabajo tan en serio dice mucho de su compromiso. No me cabe duda de que este ejercicio nos permitió a los que estamos en una posición más corporativa conectar mejor con el gemba.
Ahora estamos en la segunda fase de este experimento, en la que estamos estudiando lo que vamos a cambiar en el sistema de gestión a la luz de lo que hemos aprendido del experimento. Actualmente estamos haciendo un gran esfuerzo para mejorar el flujo de información hacia los niveles inferiores de la organización, por ejemplo.
FF: Somos bastante buenos poniendo los problemas sobre la mesa, pero tenemos que mejorar la comprensión de a quién deben ir a parar esos problemas. Ahí es donde ayudan los cuatro tipos de problemas. No tiene sentido que los operarios se ocupen de los problemas organizativos a gran escala, al igual que no tiene sentido que la dirección luche contra los incendios en la planta.
Este enfoque de la categorización de los problemas es una gran oportunidad para que gestionemos mejor la información que tenemos y la utilicemos para entender cómo atacar mejor las situaciones difíciles. No hace falta decir que nuestro papel como líderes es dar a los trabajadores de primera línea la autonomía y las herramientas que necesitan para resolver cualquier problema que encuentren.
PL: ¿Qué le ha enseñado el año pasado sobre la posibilidad de efectuar cambios cuando la mayoría de nosotros nos vemos obligados a trabajar a distancia? ¿Es posible continuar una transformación?
MFA: Hasta cierto punto, sí, pero nada va a cambiar el hecho de que hay que estar en el gemba. Ahí es donde realmente se produce la transformación. En nuestras fábricas de Colombia y Ecuador, tenemos un puesto conocido como Coordinador de Fábrica NCE. Los Coordinadores de Fábrica NCE trabajan como extensiones de mi departamento en diferentes sitios, articulando el trabajo de mejora que debe ocurrir en cada uno de ellos. En el último año han sido fundamentales para garantizar la continuidad de nuestros esfuerzos.
Con el experimento de los cuatro tipos de problemas específicos, algunos de los miembros del “equipo de mejora” dirigieron el experimento con el apoyo de los Coordinadores de Fábrica de la NCE, que se esforzaron por mantener a la gente comprometida a pesar de la distancia y la imposibilidad de reunirse. Junto con el compromiso del equipo directivo y el hecho de que los responsables de las fábricas se apoyaran mutuamente a distancia, esto nos permitió seguir adelante con nuestra transformación en medio de la pandemia.
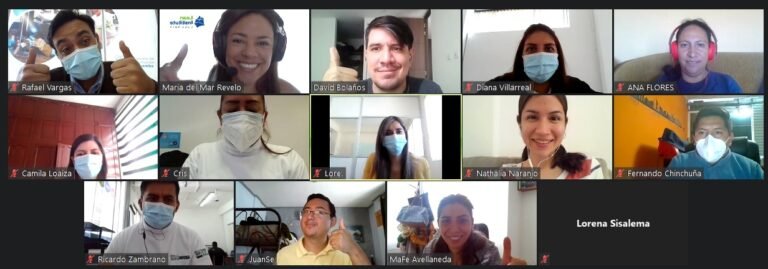
Sesión de Hansei en línea realiza por Lean Institute Colombia con el equipo de Nestlé Colombia Ecuador.
PL: ¿Dónde quieres que estén las fábricas de Nestlé Colombia Ecuador en el futuro?
MFA: Me encantaría no volver a oír de nuestros líderes que no tienen tiempo para ir al gemba porque están trabajando para resolver un problema en el que no deberían trabajar en el lugar. Y, por supuesto, me encantaría ver un progreso continuo en la aplicación del TPM y del Lean Thinking. Estamos trabajando para integrar un lenguaje diferente en nuestro trabajo diario, que sitúa la creación de valor para los clientes en el centro de lo que hacemos. Con el TPM estamos siendo más eficientes, con el Lean estamos haciendo más clara la conexión entre nuestro trabajo y el cliente. Estamos deseando continuar este experimento y ver a dónde nos lleva.
FF: Este experimento ya está dando sus frutos y estamos muy ilusionados. Si conseguimos que la empresa crezca más, podremos reinvertir parte de esos beneficios en proyectos que nos ayuden a contribuir más a la sociedad. Tenemos que mirar más allá de los beneficios y la eficiencia y definir y comunicar claramente el papel que Nestlé quiere desempeñar en la comunidad en general, por ejemplo, en lo que respecta a la sostenibilidad.
PL: ¿Qué tal su experiencia trabajando con Lean Institute Colombia?
MFA: Lo más importante para nosotros es que la relación con Lean Institute Colombia no es una relación consultor-cliente. No los veo como consultores, sino como un aliado que nos apoya en nuestro desarrollo y aprendizaje. El trabajo que realizamos juntos nos ayuda a abordar algunos de los puntos débiles de nuestro sistema, no a sustituirlo por otro diferente.
Gracias a nuestros líderes del experimento por hacer posible esta transformación:
Mery Barbosa – Fábrica de Bugalagrande
Dario Granda – Fábrica de Cayambe
David Bolaños – Miembro del equipo de Estrategia de Manufactura
Helver Ocampo – Fábrica de Bugalagrande
Augusto Maestre – Fábrica Valledupar
Juan Ortiz – Miembro del equipo de Estrategia de Manufactura
Vanessa Arias – Fábrica Sur
Fabio Ñañez – Fábrica Bugalagrande
Francisco Coy – Fábrica Bugalagrande
LOS ENTREVISTADOS:

María Fernanda Avellaneda – Gerente de Estrategia de Manufactura en T&P Nestlé Colombia Ecuador.

Fabio França – Vicepresidente Técnico Regional de T&P Nestlé Colombia Ecuador.